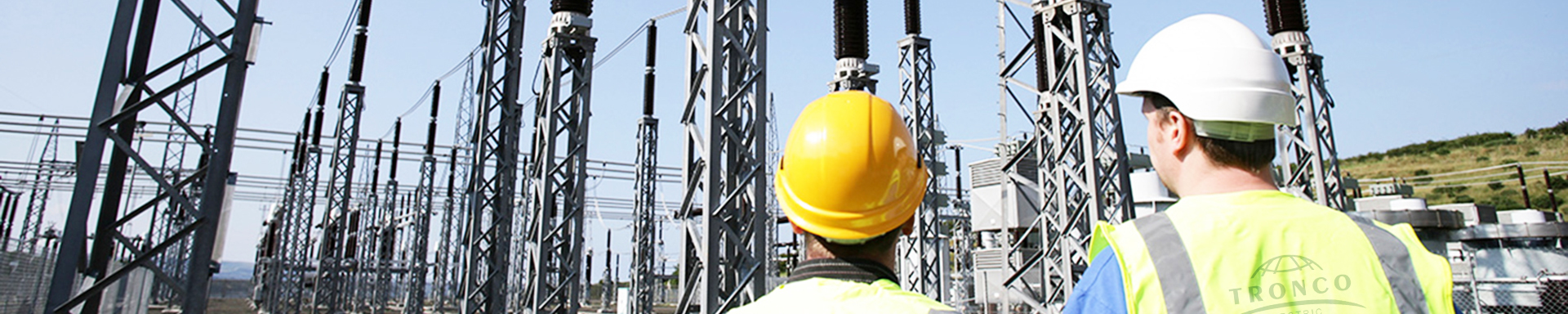
Fabrication de haute qualité d'isolants en verre trempé
2022-11-07 20:28La qualité est une mesure d'excellence et est étalonnée dans l'industrie de l'énergie électrique à l'aide d'une variété de normes nationales ou internationales telles que ANSI, IEEE, IEC, ASTM, etc. Bien que le respect de ces normes soit bien sûr essentiel, la plupart en sont venus à reconnaître que les normes ces jours-ci ne représentent plus que des exigences de performance minimales dans une application. Pour cette raison, les fabricants ainsi que les utilisateurs cherchent à différencier davantage la qualité des produits en utilisant des spécifications améliorées. La qualité passe aussi par la fabrication. À cet égard, les normes et l'amélioration continue des processus se concentrent sur les contrôles et la répétabilité dans le but de zéro défaut. En fin de compte, la qualité doit représenter la capacité et la longévité du produit en plus de la conformité aux normes de base et aux spécifications du client.
La fabrication d'isolants en verre trempé peut être considérée comme composée de deux étapes clés : la fabrication de la coque en verre, puis l'assemblage des ferrures métalliques sur cette coque. La production nécessite des équipements spécialisés et seuls quelques fabricants dans le monde disposent des ressources et de l'expérience nécessaires pour effectuer les deux étapes dans une seule installation de production. A cet égard, il est utile d'étudier la qualité non seulement en ce qui concerne la fabrication de la coque en verre trempé mais également plus tard lors de l'assemblage final de l'isolant.
La coque en verre trempé constitue l'isolant proprement dit. Bien que l'assemblage du raccord et sa cimentation soient également importants, cette coque doit rester intacte pendant toute la durée de vie afin d'assurer la fonctionnalité du produit. De plus, une fois assemblé, l'occurrence d'une rupture de coque non causée par un événement extérieur devrait être rare. Par exemple, l'industrie s'attend généralement à ce que moins de 1 unité installée sur 10 000 par an se brise spontanément. En tant que tel, l'incidence de l'auto-éclatement est un aspect de la fabrication que l'usine doit s'efforcer de minimiser.
Outre la coque critique, les composants matériels d'un isolateur en verre trempé comprennent :
1. Casquettes
Le capuchon supérieur est un raccord à douille en fonte ductile qui a été galvanisé et assemblé avec une goupille de verrouillage en acier inoxydable.
2. Épingles
Le raccord à axe inférieur est une connexion à bille en acier forgé qui a été galvanisée et recouverte de goudron bitumineux. Un collier sacrificiel en zinc peut également être ajouté pour des performances prolongées, en particulier dans les environnements de service difficiles.
Les raccords à chape/languette sont parfois utilisés à des tensions inférieures.
3. Verre brut et four
La fabrication de la coque en verre commence avec des matières premières et des ingrédients clés, notamment la silice, l'alumine, le carbonate de sodium, le sulfate de sodium, le calcaire, la potasse et la dolomite. Le calcin (parfois appelé verre germe) est du verre recyclé d'une fabrication antérieure et ajouté à ces matières premières pour assurer la cohérence d'un lot à l'autre. Le mélange de ces matériaux est spécifique à chaque fabricant et voit des variations mineures dans les éléments qui sont extraits de sources locales ou utilisés dans le four. Ces variations naturelles des minéraux expliquent la légère différence observée dans la teinte de la coque isolante en verre.
Les fours sont généralement à grande échelle avec une capacité supérieure à 100 tonnes. Pour plus de cohérence, il est important de maintenir la température et de surveiller régulièrement la chimie de la sortie ainsi que le mélange de matières premières introduites. Le four est la première source possible d'inclusions - des imperfections dans le verre qui peuvent éventuellement causer éclatement spontané. Par exemple, au fil du temps, les briques réfractaires peuvent commencer à se détacher du matériau dans le mélange de verre. Les fours doivent donc être arrêtés pour entretien toutes les quelques années et être ré-chemisés.
Formage de coquille
Cela a lieu sur une presse automatisée avec une quantité précise de paraison de verre fondu insérée dans la cavité du moule et pressée (voir Fig. 1). Les dimensions de chaque coquille particulière, c'est-à-dire la hauteur et le diamètre, sont définies par des normes, mais la géométrie et le profil de la coquille peuvent différer d'un fournisseur à l'autre.
Processus de trempe
Après le formage, la coque passe par un processus spécial par lequel elle est transférée de la presse à une ligne de trempe, en passant par un four d'homogénéisation pour maintenir le verre à une température élevée constante. La trempe du verre est réalisée en refroidissant rapidement le verre chaud à l'aide d'air comprimé à des endroits clés le long de la coque pour obtenir un refroidissement uniforme. Il en résulte que le verre a une température centrale chaude mais une surface relativement froide. La structure du verre après trempe voit le centre en tension tandis que la surface est en compression, ce qui augmente la résistance mécanique et électrique ainsi que la durabilité des parties isolantes en verre. L'obtention d'une qualité uniformément élevée dans cette étape critique nécessite un processus de manutention des matériaux hautement automatisé et soigneusement contrôlé.
Cycle thermique
Après durcissement, les coquilles sont transférées à travers un cycle thermique prescrit, où elles subissent un choc thermique dans le but d'extraire les coquilles potentiellement défectueuses. Les coques sont chauffées à environ 300°C puis plongées dans de l'eau froide, abaissant efficacement la température du verre à 120°C. Les coques en verre insuffisamment trempées s'effondreront sous l'effet du choc thermique soudain. Chaque coque est testée thermiquement au moins une fois et, si nécessaire, l'ensemble du processus peut être répété. Le cycle de choc thermique est essentiellement un contrôle de qualité clé dans la mesure où toute coque qui éclate est un"Ne pas aller"tandis que les obus qui survivent sont un 'Go'. Les coquilles de verre qui s'effondrent pendant le cycle thermique sont recyclées, avec des fragments collectés et réintroduits dans le processus de production sous forme de calcin (verre germe).
Le fonctionnement du four est"24/7"et donc plus rapide que le processus d'assemblage. Pour cette raison, les coques terminées sont conservées en stock jusqu'à ce qu'elles soient prêtes à être assemblées. Assemblage Cap & Pin Les coques en verre sont cimentées dans les bouchons tandis que les douilles de goupille et de zinc sont cimentées dans la coque avec du ciment d'alumine. Là encore, l'automatisation est utilisée pour garantir une quantité de ciment mesurée avec précision et obtenir une tolérance de longueur précise. L'assemblage cimenté est ensuite durci en cyclant à travers un bain d'une heure dans de l'eau à environ 70°C. Après durcissement, chaque isolant en verre trempé est soumis à des tests de routine électriques et mécaniques ainsi qu'à des contrôles visuels finaux.
Test électrique de routine : flashover continu pendant 4 minutes,
Test mécanique de routine : maintenu à 50 % de la cote SML pour>3 s.
Des tests d'échantillonnage sont ensuite effectués sur chaque lot d'isolateurs assemblés. Cela comprend la vérification de toutes les dimensions critiques, la conformité de la douille/de la jauge à bille, la vérification du système de verrouillage, le contrôle de la galvanisation, le test M&E et le test de perforation par impulsion.
Rapports de validation et de test
Les isolateurs finis sont soumis à des tests de conception ou de qualification conformément aux normes de l'industrie, notamment ANSI C29-2B, CEI 60383, CSA-411-1-16 et GOST 6490-93. Les clients peuvent également ajouter des critères de test supplémentaires au-delà de ces normes à leurs spécifications pour qualifier davantage les performances finales de l'isolant.
Les rapports de test pour chaque conception d'isolateur doivent être spécifiques à l'usine où l'isolateur est fabriqué. Si un fournisseur a deux usines produisant le même type d'isolateur, il doit y avoir des rapports de conception/qualification distincts pour chaque isolateur spécifique à l'usine où il a été fabriqué. Pour les produits assemblés à un autre endroit, les rapports de test pour ceux-ci doivent inclure des références à l'usine qui a fabriqué la coque. Si les coques en verre trempé proviennent de deux usines, cela doit imposer des rapports d'essais distincts (c'est-à-dire spécifiques à l'usine qui a fabriqué la coque).
conclusion
Lors de l'examen de la qualité d'un isolant en verre trempé, l'évaluation et la qualification doivent être approfondies et inclure tous les aspects de la production. Une attention particulière doit être accordée à l'endroit où la coque en verre trempé est fabriquée et également à la manière dont ce processus est maintenu pour éviter que des coques défectueuses ne soient jamais utilisées dans l'assemblage d'isolateurs finis. En effet, bien que l'assemblage du capuchon et de la broche soit important, la qualité de la coque en verre trempé aura un impact plus important sur les performances à long terme de l'isolant. Les rapports d'essai doivent être spécifiques à l'usine dans laquelle l'isolateur est produit, mais doivent également faire référence à l'endroit où la coque a été fabriquée. Cela nécessiterait des marquages d'usine spécifiques. Au minimum, la coque en verre trempé doit avoir des marques moulées dans son corps, y compris la cote M&E, la référence du code de lot, et l'identification de l'usine (ID). Ces marquages doivent être lisibles et permanents. L'ID de l'usine où l'isolateur est assemblé doit être marqué sur le capuchon de l'isolateur - également lisible et permanent. Même lorsqu'ils sont fabriqués dans la même usine, le fait d'avoir de tels marquages à la fois sur la coque et sur le capuchon permet d'identifier quand la coque a été fabriquée et quand elle a été assemblée. L'ajout de marquages d'identification d'usine à la coque est simple, avec peu d'impact sur le coût du produit, mais il apporte un niveau d'assurance qualité plus élevé pour les isolateurs. Les diverses normes de l'industrie (par exemple ANSI, IEC, CSA) n'exigent pas spécifiquement l'identification d'usine sur une coque, mais devraient peut-être le faire. Même lorsqu'ils sont fabriqués dans la même usine, le fait d'avoir de tels marquages à la fois sur la coque et sur le capuchon permet d'identifier quand la coque a été fabriquée et quand elle a été assemblée. L'ajout de marquages d'identification d'usine à la coque est simple, avec peu d'impact sur le coût du produit, mais il apporte un niveau d'assurance qualité plus élevé pour les isolateurs. Les diverses normes de l'industrie (par exemple ANSI, IEC, CSA) n'exigent pas spécifiquement l'identification d'usine sur une coque, mais devraient peut-être le faire. Même lorsqu'ils sont fabriqués dans la même usine, le fait d'avoir de tels marquages à la fois sur la coque et sur le capuchon permet d'identifier quand la coque a été fabriquée et quand elle a été assemblée. L'ajout de marquages d'identification d'usine à la coque est simple, avec peu d'impact sur le coût du produit, mais il apporte un niveau d'assurance qualité plus élevé pour les isolateurs. Les diverses normes de l'industrie (par exemple ANSI, IEC, CSA) n'exigent pas spécifiquement l'identification d'usine sur une coque, mais devraient peut-être le faire.